THE WORLD’S LARGEST AIRCRAFT MANUFACTURER USES INTERIOR ARCHITECTURE TO INCREASE PRODUCTIVITY, SAVE COST, AND HAVE A POSITIVE IMPACT ON WORK CULTURE
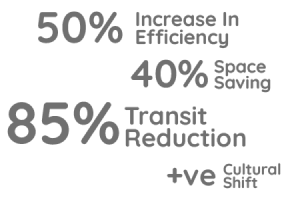
In the wake of 9/11, Boeing found itself in a race to implement lean manufacturing processes. Opting to use interior architecture as a tool to solve business problems, Boeing engaged Steelcase consulting team and architectural design firm NBBJ to design a new workplace to mesh with the cultural shift towards enhanced collaboration.